neodymium magnet (also known as NdFeB, NIB or Neo magnet), the most widely used type of rare-earth magnet, is a permanent magnet made from an alloy of neodymium, iron and boron to form the Nd2Fe14B tetragonal crystalline structure. Developed in 1982 by General Motors and Sumitomo Special Metals, neodymium magnets are the strongest type of permanent magnet commercially available. They have replaced other types of magnets in the many applications in modern products that require strong permanent magnets, such as motors in cordless tools, hard disk drives and magnetic fasteners.
Alnico is an acronym referring to a family of iron alloys which in addition to iron are composed primarily of aluminium (Al), nickel (Ni) and cobalt (Co), hence al-ni-co. They also include copper, and sometimes titanium. Alnico alloys are ferromagnetic, with a high coercivity (resistance to loss of magnetism) and are used to make permanent magnets. Before the development of rare earth magnets in the 1970s, they were the strongest type of magnet. Other trade names for alloys in this family are: Alni, Alcomax, Hycomax, Columax, and Ticonal.
The composition of alnico alloys is typically 8–12% Al, 15–26% Ni, 5–24% Co, up to 6% Cu, up to 1% Ti, and the balance is Fe. The development of alnico began in 1931, when T. Mishima in Japan discovered that an alloy of iron, nickel, and aluminum had a coercivity of 400 oersted (Oe; 32 kA/m), double that of the best magnet steels of the time.
Ferrite magnet is a type of ceramic compound composed of iron oxide (Fe2O3) combined chemically with one or more additional metallic elements. They are both electrically nonconductive and ferrimagnetic, meaning they can be magnetized or attracted to a magnet. Ferrites can be divided into two families based on their magnetic coercivity, their resistance to being demagnetized.
Samarium cobalt (SmCo) magnet, a type of rare earth magnet, is a strong permanent magnet made of an alloy of samarium and cobalt. They were developed in the early 1970s by Albert Gale and Dilip K. Das of Raytheon Corporation. They are generally ranked similarly in strength to neodymium magnets,but have higher temperature ratings and higher coercivity. They are brittle, and prone to cracking and chipping. Samarium–cobalt magnets have maximum energy products (BHmax) that range from 16 megagauss-oersteds (MGOe) to 33 MGOe, that is approx. 128 kJ/m3 to 264 kJ/m3; their theoretical limit is 34 MGOe, about 272 kJ/m3. They are available in two “series”, namely Series 1:5 and Series 2:17.
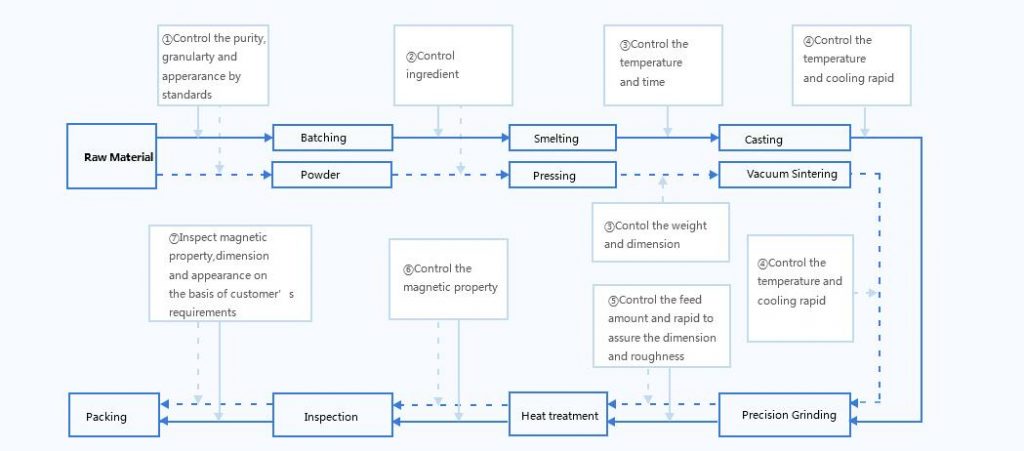
Magnet manufacture process can be divided to sintering, casting and injection molding generally. Each element will have influence on final magnetic materials, such as our new technical breakthrough for alnico KM500 to KM600, titanium element is amazing to increase the resistance of magnetic loss with change parameter for Hcj, related Hcb as well, our technical team is working on a video to illustrate each process in manufacturing, which will be coming soon!
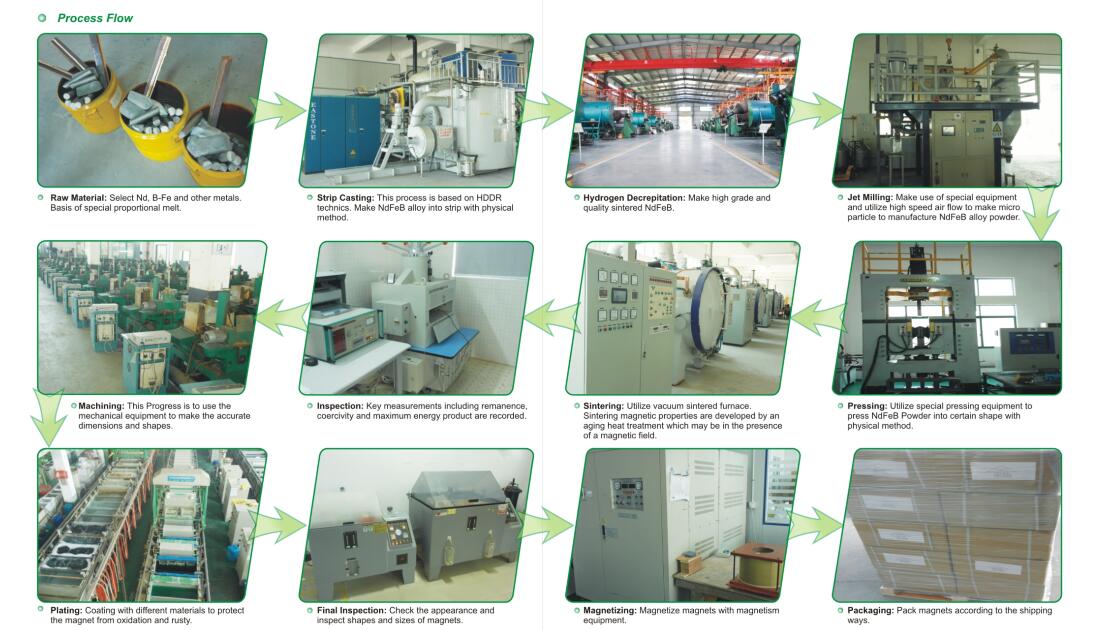
Magnet Manufacturing Quality Control
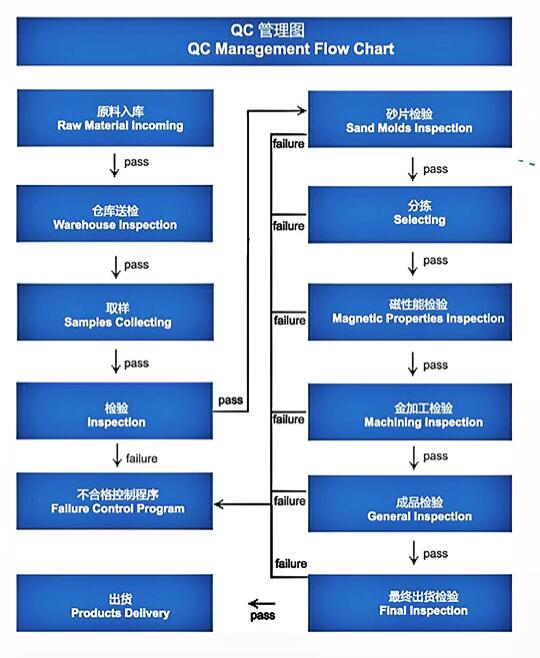